The approach is the integration of high electron mobility, high magnetic sensitivity 2DEG structures with on board analogue and digital electronics to deliver scanning and 2D arrays magnetic imaging systems for Non-Destructive Testing of metallic and composite materials. Recently fully integrated QWHE circuits have also been attempted.
Lead: Prof M.Missous (m.missous@Manchester.ac.uk)
Contributing Academics: Dr M. Migliorato
Overview: The overarching theme of WP7 is magnetic imaging of ferrous, non-ferrous materials and composites. The work follows a vertically integrated approach starting from epitaxial growth of advanced 2DEG structures with tailored magnetic sensitivities to device fabrication of integrated arrays , circuits and passives, packaging and finally system integration for imaging of flaws, defects and microstructures (See Figure below).
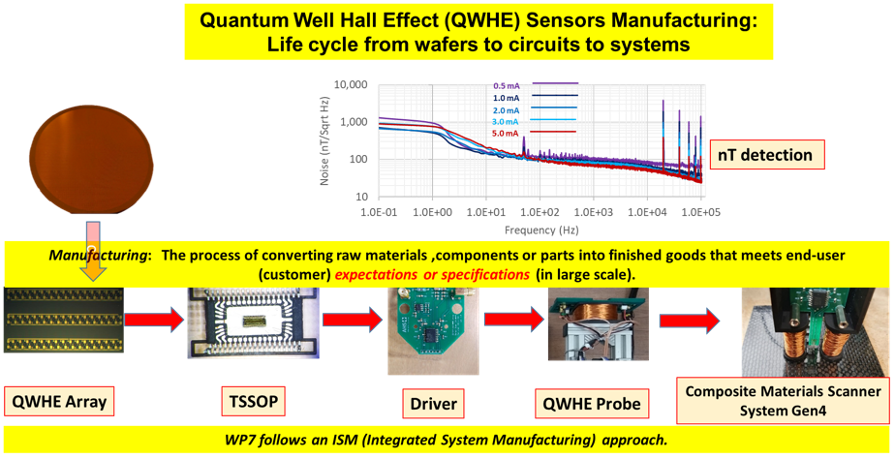
Progress and Challenges: During the period magnetic imaging modality using Quantum Well Hall Effect sensors (QWHE) for were extended to study composites including both physical defects and fiber detection and imaging using a novel technique we term QW-ECFM. We have designed and delivered numerous system demonstrators with key challenges being imaging and classifications of flaws and defects in metals and composites.
Impact has been very strong as demonstrated in 7, separate, fully funded collaborative IUK , NZTC and EU Horizon projects with [Renishaw, TWI, EtherNDT, FarUk, Wright, Home office, BAESystems, Rolls Royce] in imaging defects from corrosion under insulation in steel to flaws and fibers in composites and high value steel.
Recent work has concentrated on fully integrated circuits using the QWHE sensors as active transistors. This has allowed development of a complete Process development Kit (PDK) for the design and fabrication of circuits that are compatible with harsh environment operations (both in temperature spans and radiation hardness) see Figure below. Challenges remain in balancing performance with wide range temperature operation, from cryogenic to > 200 °C .
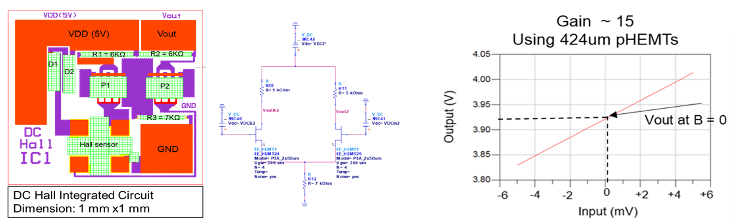